Can Dual-Zone Powder Coating Ovens Handle Mixed Material Loads Efficiently
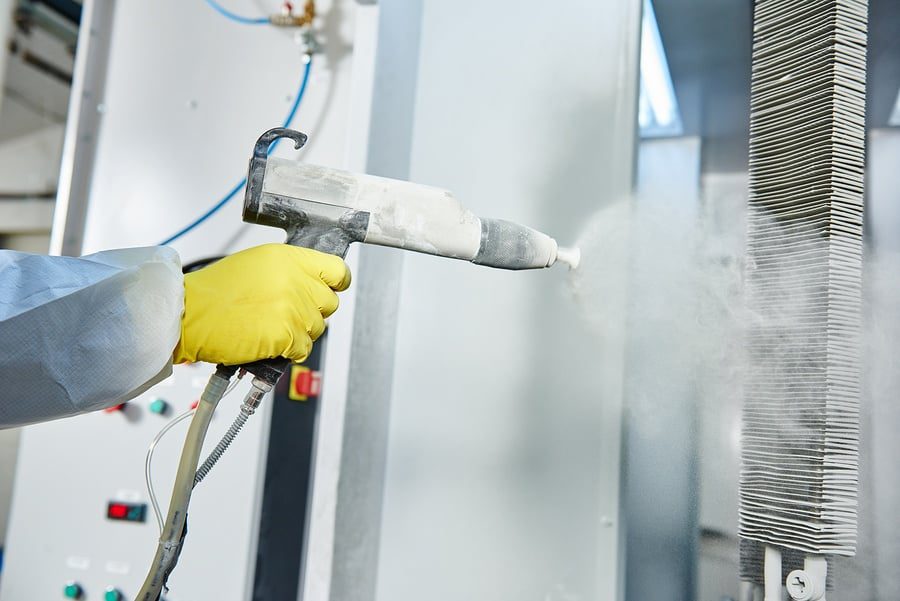
When it comes to finishing processes, powder coating stands out as a reliable and durable solution for protecting and beautifying various materials. But what happens when your workload includes mixed materials that require different curing conditions? Enter the dual-zone powder coating oven, a marvel of engineering that promises to handle such challenges with precision. Can it truly deliver? Let’s break it down and uncover what you might not know about these versatile machines.
Managing Diverse Thermal Profiles with Precision for Mixed Materials
Not all materials are created equal—some demand higher curing temperatures, while others require a gentler approach. Dual-zone powder coating ovens are designed to handle these disparities by dividing the oven into separate zones, each with its own temperature controls. This design enables the oven to cater to the specific thermal needs of each material type simultaneously.
For instance, metals with high heat tolerance can be cured in one zone, while heat-sensitive substrates like plastics or composites can occupy the other. The result? Precise thermal management ensures that each material receives the right treatment without overheating or under-curing. This capability not only preserves the quality of your coatings but also reduces waste and rework.
Synchronizing Heat Distribution to Prevent Coating Inconsistencies
One of the most common challenges in powder coating is achieving a uniform finish, especially when dealing with mixed materials. Uneven heat distribution can lead to problems like bubbling, peeling, or inconsistent color. Dual-zone powder coating ovens address this issue by synchronizing heat distribution across zones.
Each zone’s temperature is carefully calibrated to ensure that coatings cure evenly, regardless of the material’s thermal properties. Advanced airflow systems within quality powder coating ovens also help maintain consistent temperatures, eliminating hotspots or cold spots. The result is a flawless finish on every item, whether you’re working with steel, aluminum, or delicate composites.
Adapting to Varying Substrate Properties with Independent Zone Controls
Every substrate comes with its quirks. Metals expand differently under heat compared to plastics, and each material reacts uniquely to powder coating processes. Dual-zone ovens excel in adapting to these differences, thanks to their independent zone controls.
This independence allows operators to fine-tune settings for each zone, catering to the specific needs of the materials being processed. For example, one zone can operate at a high temperature for rapid curing of metals, while the other maintains a lower setting to protect heat-sensitive components. Reliable powder coating ovens equipped with such flexibility minimize the risk of damage and maximize efficiency.
Optimizing Curing Efficiency Without Compromising Material Integrity
Curing efficiency is crucial in any powder coating process, especially when dealing with high production demands. However, speed should never come at the cost of material integrity. Dual-zone ovens strike a delicate balance by optimizing curing times without compromising the structural properties of the materials being coated.
For manufacturers juggling mixed material loads, this efficiency means faster turnaround times without sacrificing quality. Compact powder coating ovens with dual-zone capabilities are particularly advantageous for businesses with limited floor space, as they pack high performance into a smaller footprint while maintaining exceptional results.
Reducing Operational Downtime by Processing Multiple Materials Simultaneously
Switching between materials with different curing requirements can be time-consuming, especially in a single-zone oven. Every change means adjusting temperatures, waiting for the oven to stabilize, and potentially halting production. Dual-zone ovens eliminate this bottleneck by allowing you to process multiple materials simultaneously.
With separate zones handling different curing conditions, there’s no need to stop and reset the oven for each batch. This reduction in downtime translates to higher productivity and lower operational costs. Reliable powder coating ovens that support such efficiency are game-changers for manufacturers striving to meet tight deadlines and high-quality standards.
Achieving Seamless Transitions Between Zones for Flawless Finishes
Transitioning from one zone to another can be tricky, especially when different materials are involved. Poor transitions can cause uneven curing or compromise the final finish. Dual-zone ovens are designed with seamless transitions in mind, ensuring smooth airflow and consistent temperatures throughout the oven.
Whether you’re working with compact powder coating ovens or larger models, this capability ensures that every item receives consistent treatment, even as it moves between zones. The result is a flawless finish that meets the highest quality standards, no matter how complex your workload.